CUSTOMER SUCCESS STORIES
Unlocking Reliability Excellence at Unilin Panels
FROM UNPLANNED DOWNTIME TO PLANNED INTERVENTIONS
Unilin Panels' vision towards production reliability
Unilin Panels, part of the Unilin Group and a subsidiary of Mohawk Industries, Inc., is a leading producer of sustainable, high-quality wood-based solutions for the construction and interior sectors. Operating primarily in Europe, their products include chipboard, MDF panels, HPL, and melamine faced boards.
In the chipboard production process, recycled wood particles are bonded with adhesive resins under high pressure and temperature. Reliability management is crucial to prevent unplanned downtime and issues that could compromise overall product quality.
As a leader in the sustainable chipboard industry, Unilin Panels has implemented an innovative reliability and maintenance strategy that reduces environmental impact and delivers high-quality products. Partnering with VersaSense, they have deployed AI and IoT-based solutions at their Bospan and Spano facilities, transforming downtime into valuable insights and planned interventions.
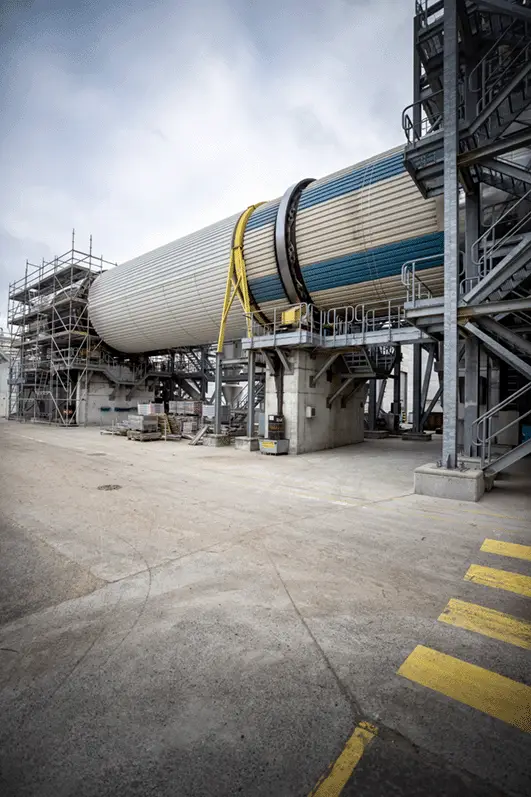
CHALLENGES
Harsh manufacturing environment, diverse machines, unplanned downtime
As part of its reliability strategy, Unilin Panels wanted to reduce unexpected downtime. Unplanned downtime causes a significant financial impact and disrupts both upstream and downstream operations of the continuous production process, while also affecting overall production quality.
To combat unexpected machine failures, it was crucial to implement continuous monitoring on a variety of machines throughout the production facility. These emcompass standard rotating machinery such as pumps, fans, and electric motors, as well as intricate systems like redlers and elevators.
The primary objective was to assist first-line maintenance operations by providing a clear, easily understood, and continuous assessment of the health of a large fleet of various and complex machines. Traditional routine checks happen throughout the plant, but they are not always possible to perform during regular production and may therefore overlook certain issues. Simplified scoring and reporting, based on diverse algorithms, indicate potential issues and provide clear calls to action, guiding experts towards areas requiring further inspection.
SOLUTION
Factory-wide network of self-organising wireless IoT sensors
To support the reliability team in continuous asset monitoring and health predictions across the entire facility, Unilin Panels decided to engage with VersaSense to address the predictive maintenance challenge.
VersaSense deployed a highly robust and secure wireless mesh network. This network comprises hundreds of battery-powered wireless sensors installed on various machines and dedicated to monitoring vibration and temperature around the clock.
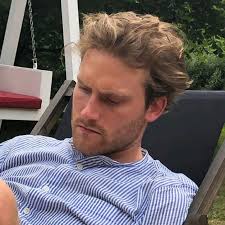
VersaSense sensors are fully self-organising and equipped with secure over-the-air reconfiguration capabilities. This enables fine-grained configuration of every software aspect on the sensor as needed. Thus, for example, new or specialised algorithms for vibration signal analysis or pattern recognition functionality can be effortlessly deployed for specific machines whenever necessary.
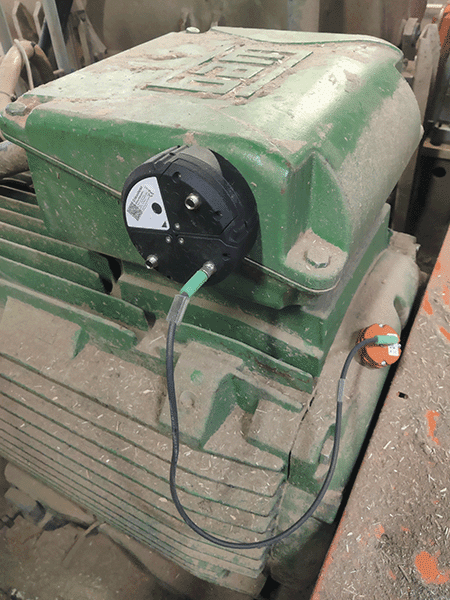
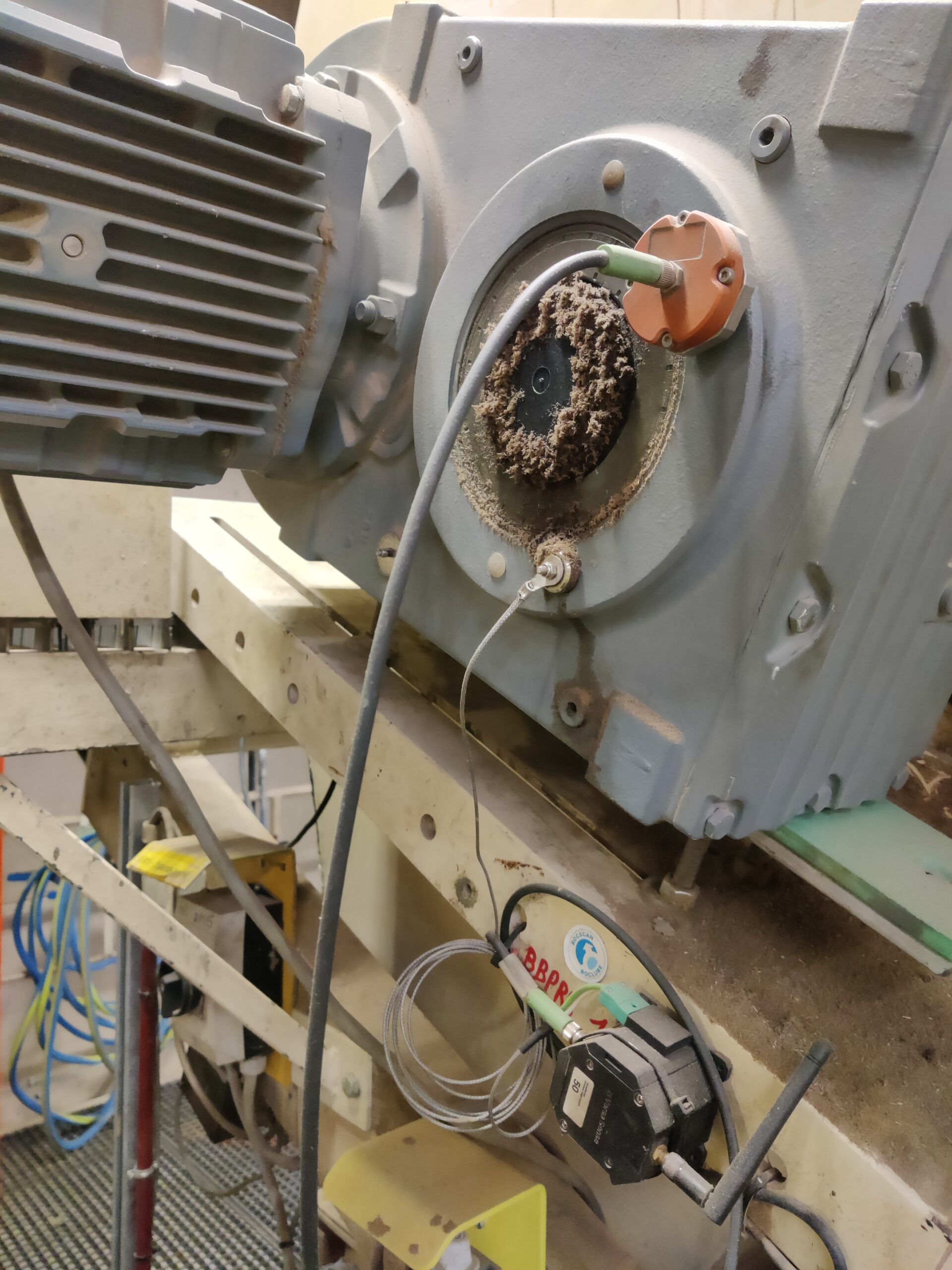
24/7 continuous monitoring of machine health
The reliability team installed sensors on a range of machines, such as pumps, saws, compressors, fans, redlers, and conveyor belts. Each sensor was set up to regularly gather vibration and temperature data and fully analyse it locally. The collected vibration measurements undergo comprehensive on-sensor processing, including examination of time-domain metrics and full spectral analysis, to detect any anomalies attributed to machine or bearing wear.
Through an intensive focus on combining sensor and production data with and AI-driven predictions, the system autonomously uncovers machine regimes within the data, contributing to a comprehensive understanding of the machine itself.
sensors installed
on 2 chipboard
production sites
sensor measurements
analysed per plant
per year
machine issues
flagged in first
6 months
Enhanced insights through AI-driven machine health assessments
All collected measurements are transmitted to the VersaSense Enterprise IoT platform, where AI-driven software performs trend analytics, anomaly detection, and pattern recognition of previously known failures. The platform not only presents users with a straightforward representation of machine health but also furnishes machine experts with the details necessary for further in-depth analysis.
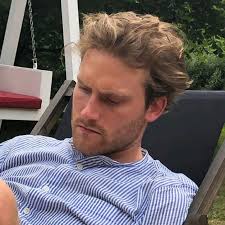
The reliability team has the flexibility to include feedback on detected issues and maintenance operations that were performed, allowing the system to recognise patterns and retrain when required. Furthermore, the platform facilitates machine-to-machine comparisons, providing insights into behavioural patterns relative to similar machines.
Finally, a major requirement was to swiftly integrate health predictions with the existing in-house IT/OT systems, allowing Unilin to link these results to the current production context. This interconnected approach enhances the overall understanding of the machinery’s performance in the broader manufacturing landscape.

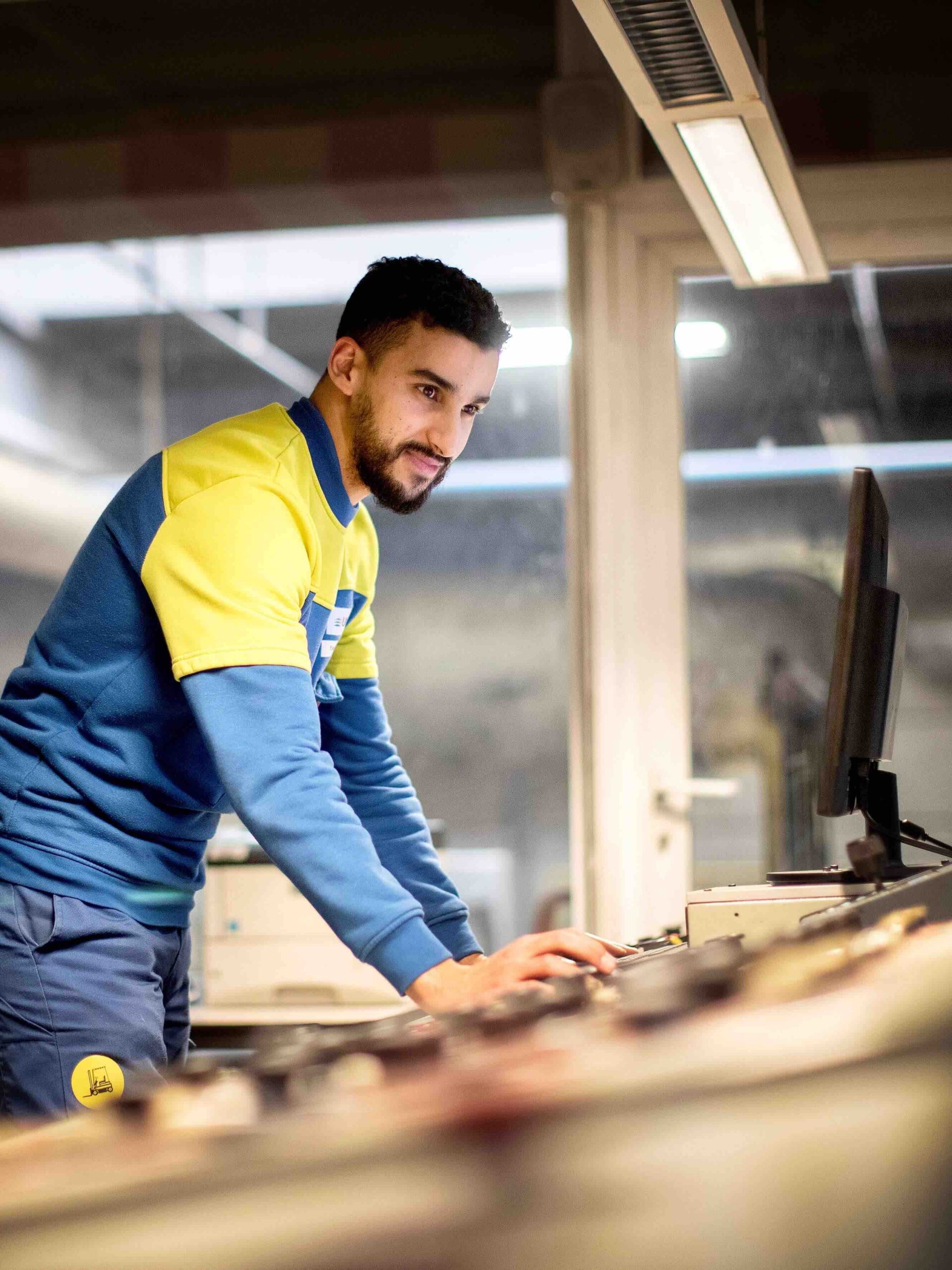
RESULTS
Modern Reliability Management. Less unplanned downtime.
In the first few months following the installation of the initial sensors, VersaSense’s AI-assisted predictive maintenance solution enabled Unilin Panels to prevent several incidents and significantly transform their maintenance operations. Through continuous 24/7 monitoring of machines and analysis of vibration and temperature data captured every 5 minutes, Unilin Panels can seamlessly identify typical machine regimes and anomalies, providing insights into required maintenance actions.
This proactive approach has led to a substantial reduction in unplanned downtime. Being able to timely plan maintenance interventions and minimising surprise disruptions to production schedules saved tens of thousands of Euros not only in production time and quality, but also in major replacement costs by preventing equipment failures before they escalate to disaster.
Moreover, the cloud-based platform offered by VersaSense has played a important role in improving overall equipment effectiveness (OEE) at Unilin Panels. The trend analytics and anomaly detection functionalities provide a deeper understanding of machinery health, empowering the reliability team to make more informed decisions. Technical engineers receive daily health assessments and detailed insights into the evolution of machine performance over time. Additionally, the system enables them to evaluate the effectiveness of their maintenance actions.
In addition, the capacity to provide feedback on maintenance operations, retrain the system, and compare machines with each other further enhances Unilin Panels’ ability to optimise their production processes. This fosters a more resilient and efficient manufacturing environment.